
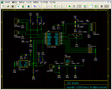 |
We manufacture a wide array of printed circuit boards, from single-sided boards to multilayer and flexible boards. Thanks to our accumulated expertise and highly reliable design capability, we are able to satisfy customer needs through services including system design, circuit design, printed circuit board design, and pattern design. |
|
 |

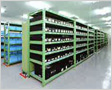 |
We deal with hundreds of major manufacturers of electronic components, allowing us to select and procure the components that best meet each application’s needs. Electronic components are stored in areas equipped with robust anti-static systems, and we have built a highly reliable environment for their handling, starting at the component inventory control stage. |
|